【ものづくり最前線 国産ルネサンス】イージーオーダースーツの花菱縫製 カスタマイズの技術生かす 車椅子利用者用オーダースーツ開発
若い世代にも注目され、市場規模が拡大する中、新規参入企業が増えて競争も激化しているオーダーメイドスーツ業界。
80年以上の歴史があるイージーオーダー(EO)スーツの花菱縫製は「どんな人にもスーツを楽しんでもらいたい」(野中雅彦社長)との思いから開発した車いす利用者向けオーダースーツが差別化の大きな武器になりつつある。長年取り組んできた一人ひとりの要望を聞きカスタマイズ対応しながら量産化する仕組みと技術力が背景にある。
【関連記事】花菱縫製 車椅子利用者用オーダースーツ 女性向け開発
花菱縫製は1935年に創業。国内の自社工場で縫製する。生産能力はスーツ換算で1日当たり500着、年間約13万2000着。従業員数は約560人。埼玉県の岩槻工場(138人)をベースに、アイテムごとに生産を振り分ける。
紳士・婦人のジャケットやベスト、紳士コートを生産する宮城県の白石工場(従業員数101人、年間生産数量5万7000着超)、紳士ジャケット・コートの群馬の新前橋工場(142人、6万8000着超)、紳士・婦人パンツの山形県の白鷹工場(88人、12万3000超着)、ドレスシャツとパンツの岩手県の江刺工場(74人、ドレスシャツ6万3000枚、パンツ1万4000本弱)などがある。
一着ずつ管理
オーダーの要となる岩槻工場は本社機能のほか、生産前準備・裁断と仕上げを担う。8月前半は秋物立ち上がりの直前なので工場内のスペースが生地で埋め尽くされる。オーダースーツ特有の店頭ディスプレーのため、反物だけでなく、1着分(3.2メートル)に裁断した生地が所狭しと並ぶ。
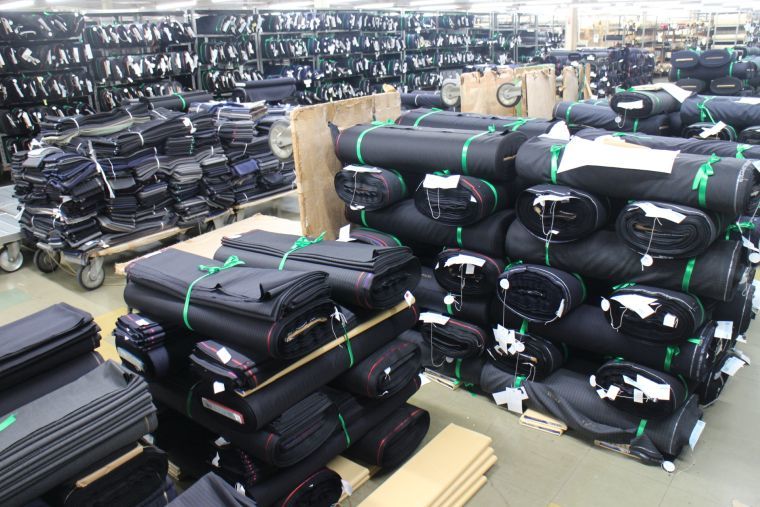
通常、オーダースーツを仕立てる際、店頭から送られてくる採寸書をデータ入力し、自社ストックの生地と付属(裏地、ボタン、芯地、ゆきわた、糸など)の基本セットを組み合わせる。客一人ひとりが全て違う型紙や仕様によって生産するので、一着ずつの管理が重要となる。
その次の工程では、CAD・CAM(コンピューターによる設計・生産)を駆使するが、型紙を設計する場合でも生地のキズ部分を省き無駄のないようにパーツをはめ込む。基本的に自動化しているものの、最終的には機械を扱う現場の人間の経験が大事になってくる。
裁断も9割弱が機械で1割強が手作業になる。とくに格子柄を襟と背中などのパーツ同士で合わせるには人の力が必要になる。トライアル中ではあるが、新規に柄合わせができる自動裁断機を導入し、さらなる正確さとスピードアップを追求している。
裁断された生地が各縫製工場で仕立てられ、再び岩槻工場に戻ってくる。仕上げでは袖・背・肩・ラペルなど部分ごとに独自開発されたプレス機と熟練職人の手作業のアイロンワークによって立体的なシルエットを作り出す。
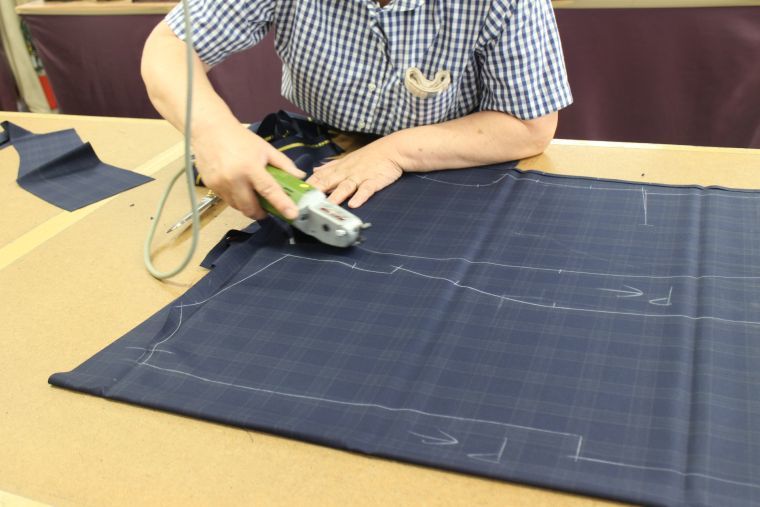
量産を可能に
生産前準備・裁断と仕上げ以外に縫製スペースもある。タキシードやモーニング、燕尾(えんび)服、サンプルなど特殊な服作りに対応する。数人の多能工が手掛ける。ここで車椅子利用者用オーダースーツも生産する。これまで難易度の高い補整にも対応してきたオーダーメイドで培ってきた技術力と柔軟な対応力があったため、今回の新たな取り組みについても、現場の職人たちは抵抗感なく着手できたという。通常のスーツと異なり、座位姿勢を基準に設計し、車いすをこぐ動作、着脱のしやすさに配慮し、見栄えと着心地を追求した。
研究・開発に1年をかけ、自社の国内工場の通常と同じラインで量産を可能にしたため、特殊なパターンやディテールにもかかわらず、5万円以下というリーズナブルな価格設定が可能となった。
紳士の車椅子利用者用オーダースーツはスタートから1年が経過し、直営店(全19店のうち6店)で約100着を販売した。スーツの用途はビジネスが7割、フォーマルが3割の状況だ。
今秋冬には要望が多かった婦人版もスタートする。「ケガや病気で歩行が困難な人だけでなく、高齢化社会への対応としても車椅子利用者向けの商品開発はトライする意義は大きかった」という。
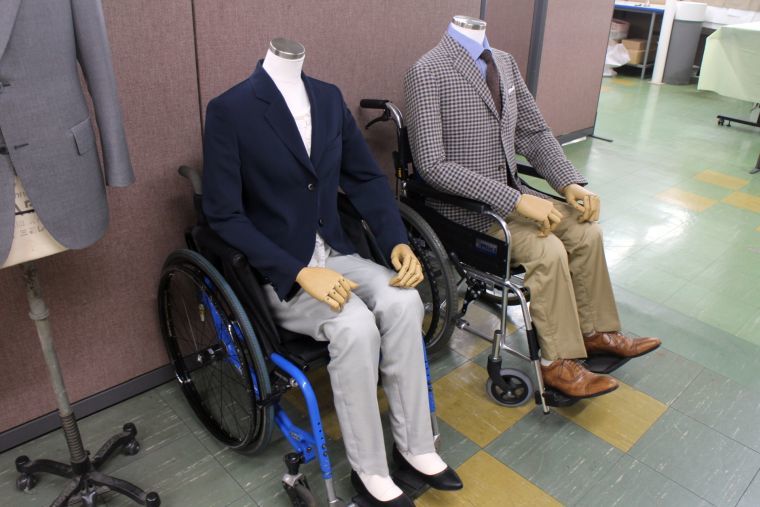
《チェックポイント》試作を繰り返して商品化
車椅子利用者用オーダースーツの仕様は、ジャケットは裾がめくれ上がらないように丈の長さやボタン位置、フロントカットを変え、腰ポケットの傾斜を強くし、ベントをなくした。こぐ動作を意識して袖付け回りの外周寸法を通常品より大きくし、袖先や脇下部分を人工皮革で補強した。スラックスはひざ裏に3本のダーツを入れ160度に屈曲させることでだぶつきを防ぎ、すっきり見せる。ウエストは脇ゴム仕様で、フロントは面ファスナー仕様にした。
そのほか、パンツの前側を浅く、後ろ側を深くしてシャツを出にくくし、ファスナー止まりを深くしたことで着脱や小用時の負担を軽減した。床ずれ防止に後ろポケットをなくすこともできる。研究・開発では、パラリンピックのメダリストなど車いすアスリートをはじめ、国立障害者リハビリテーションセンターにも協力してもらい、様々な車椅子利用者から意見を吸い上げ、試作を繰り返して商品化にこぎつけた。
《記者メモ》究極のカスタマイズ
車椅子用スーツ商品開発を量産ラインに乗せるまでが大変だったが、通常の服作りよりも手間はかかるものの、現場での縫製はスムーズに対応できたという。オーダースーツとしてパーソナルな要望に真摯(しんし)に応えてきた技術の蓄積があるからだろう。 野中社長は「自社の国内縫製工場の技術によって公平な社会の実現に貢献したい」との思いが強く、さらに難易度の高い婦人の車椅子利用者用オーダースーツの開発にも着手した。 こうした〝究極のカスタマイズ〟に挑戦し続けることで、既存のスーツでの新商品の開発やさらなる品質の向上にもつながっていく。その結果、世界でも勝負できる工場になりうるはずだ。
(大竹清臣)
(繊研新聞本紙8月22日付)