傘にこだわり続けてきた伝統と歴史あるオーロラ。新潟県胎内市黒川の洋傘工場「新潟センター」は国内で唯一の洋傘工場で、高い技術で1本1本手作業による美しい張りのある傘に仕上げ、消費者に届けている。1896年の創業から傘作りの追求が始まり、1970年に東京・青戸の自社工場を現在の新潟に移し、さらに機能性や素材など洋傘の日進月歩の進化を追い続けながら、魅力ある傘を生産し続けている。
新潟センターの洋傘生産量はコロナ禍前の実績で、月産1万本、年間では約12万本。オリジナル加え、「アクアスキュータム」や「ニナリッチ」などのライセンスブランドの生産も手掛けている。現在、傘の製造に携わる人員は25人。加えて子育てなどによる在宅での内職や工場設立当時の職人などの力も借りながら、1本1本を丁寧に作り上げている。
18ほどの工程が必要
傘の主な生産工程は生地に光を当ててプリントやコーティングのムラ、傷をチェックする検反から始まり、生地の縁がほつれないようにミシンをかける縁かけ。そして、製造する洋傘の仕様に合わせた木型を作成し、生地を三角形にコマ裁断、生地を親骨の本数に応じてコマとコマを縫い合わせる中縫い。ネーム布や手元などの製造、三角形のコマをつなぎ合わた傘カバーの中心を縫製する天かがり、傘骨に傘生地カバーを縫い合わせる中綴(と)じなどを経て、手元取り付けとなる。工程の間には何度も検品作業があり、18ほどの工程を通して1本の洋傘が出来上がる。
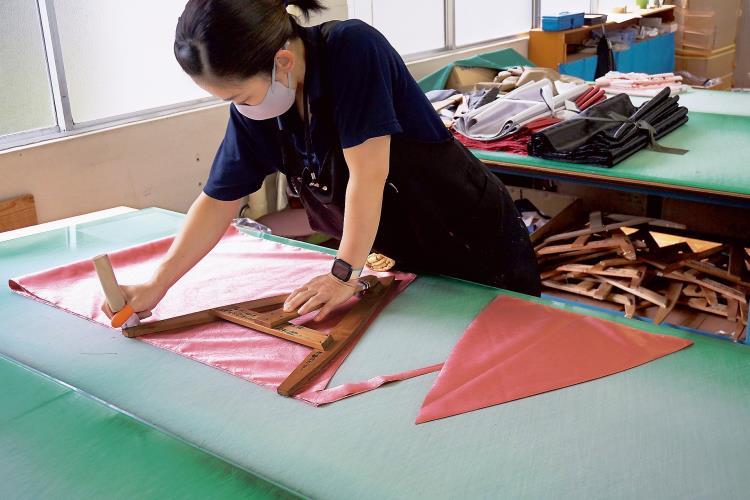
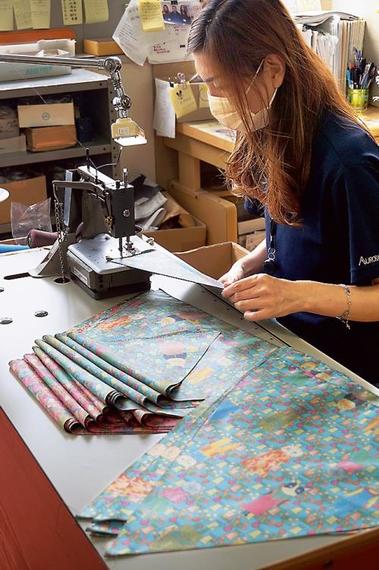
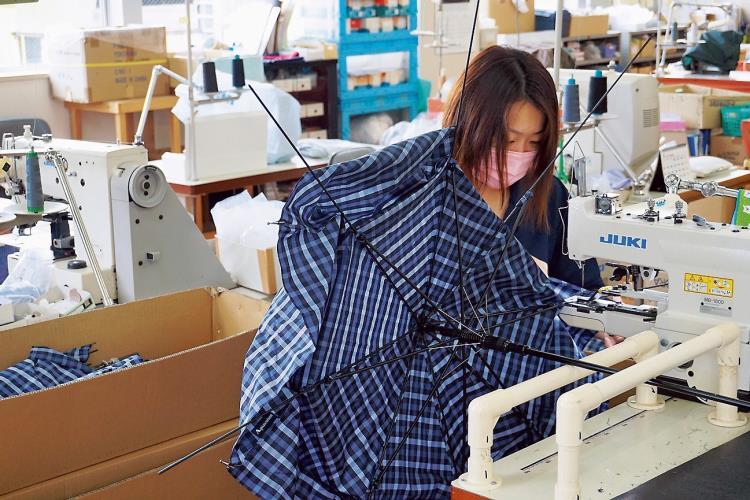
多くの工程を経て出来上がる傘で重要になるのが木型で、傘生地カバーの三角形のコマ裁断の基となるもの。生地のしわを防ぎ、美しいフォルムに仕上げるため、傘のしずくが流れ落ちる道の「谷落ち」、裾の弧を描く曲線の「クリ」のバランスを適度に保つためには木型の出来が重要になってくる。現在、木型を製作するのは新潟センター長代理の小野貴史さん一人。入社12年目で、傘の製造に携わって10年になる。携わる当時は60代の木型を作れる職人が2人ほど在社し、日々勉強しながら技術を磨いてきた。
木型は伸縮など特徴が違う生地や骨の本数などによって、試作を何度も繰り返し微調整しながら作っていく。シーズンごとにデザインや素材などが変わるため、その度に木型を試行錯誤しながら作り上げていく。以前はポリエステルやナイロン生地が支流だったが、「最近は多様なニーズに応えるため、生地も多様になっていて、製造泣かせ」という。
日傘の綿・麻混やラミネート素材使いで表と裏地の伸縮率が違う晴雨兼用などは、より微調整が必要。これまでに使用した多くの木型がストックとしてあるが、常に新しいものを作り上げる必要がある。だがここで手を抜くと、「傘を開閉したときの生地のフォルムやバランスに影響し、故障の原因にもなる」ため、「何年経験を積んでも、毎日が勉強で、経験が通じないものもある」という。
機能設備では工場に撥水(はっすい)などを検証する検査室を設けている。社内基準は認証基準より高く設定し、初期不良の危険性を回避するようにしている。
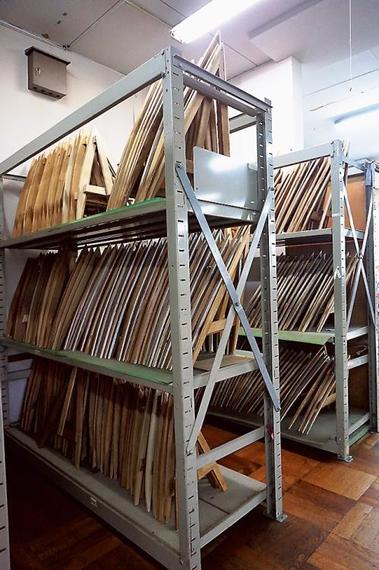
小ロット生産も強みに
工場のスタッフは現在、40代を中心に20代の若手から50、60代の社員とパート社員で生産を担っている。3~5年でようやく手に職が就き、一つの工程を任せられるようになる。多くの工程をラインごとに分けて作り上げているが、「1本を作り上げる作業工程を多く人が受け持つことで、どうしても個体差がでてくる」ため、限りなく少ない人の手で作り上げられるようにしていきたいという。
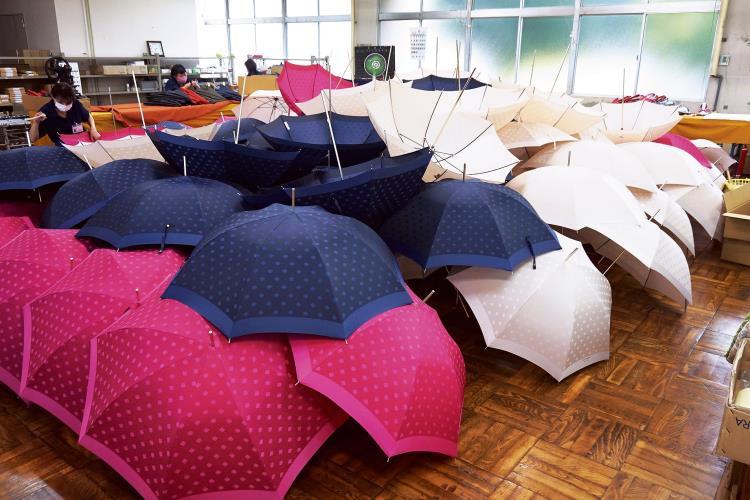
少量やオリジナル、別注商品の生産依頼に応えられることも強みで、数本単位でも生産を請け負う。小野さんは「少量生産の方が個体差が減り、品質も上がる」と、より100%に近い状態で生産できる小ロットは工場の大きな特徴で、メリットと強調する。
一方、傘作りでは縫製技術や経験などが必要となり、簡単には世代交代が難しい状況にもある。工場は「職人や熟練の経験が傘作りを支えている」ため、技術を磨き、伝統を継続していくために人材教育にも力を入れている。
デザイナーや商品担当者は多様なニーズや環境変化などに応える新しい企画を打ち出す。軽量化や撥水機能、遮光性、抗菌など、毎シーズン進化する企画に応えるためには、日々の勉強は欠かせない。「傘はこういうもの」「これは出来ない」など、固定概念にとらわれていては先に進まないという。あえて、製造過程などを知らない担当のアドバイスや視点がもの作りに生かされることもある。職人も経験を生かしながらも柔軟な思考が必要になっている。学んだものを単に引き継いでいくのではなく、「職人任せではなく、色々な人とディスカッションしながら、人材を育てていきたい」という。
《記者メモ》目立たない所で日々進化
洋傘は見た目はあまり変わらない形状をしているが、骨組みの数や機能性、新素材の採用、軽量化などニーズや環境変化に対応するため、日々進化している。職人技が工場を支えている面も多いが、多くの工程で新しいことにチャレンジしている。
緊急避難的な要素も強い洋傘において、安価なビニール傘の広まりで使い捨てのイメージが強い。一貫して量産される傘とは違うものづくりへのこだわりを続け、長く愛されるような傘づくりに「洋傘工場を持ち続ける誇りがある」という。
だからこそ、技術の継承を大切にしながら、消費者に傘への興味や良さをどう伝えていくかも大事なっているという。新型コロナで、よりブランドや商品の背景に共感し良いものを長く使いたいとの購買が増えている。ものづくりへのこだわり、探求心を高めて市場に提供し続けて欲しい。
(古川伸広)
(繊研新聞本紙21年9月8日付)