【ものづくり最前線】東レのダウンリサイクル 世界にない機械、自ら開発 生産性向上へ地道な努力
東レは今年5月から瀬田工場(滋賀県大津市)で、使用済み製品からダウンを分離回収する一貫自動装置を稼働させた。ユニクロの店頭で集めたウルトラライトダウン(ULD)を再び製品にするリサイクルプロジェクトで、最も肝となる工程だ。世界にない設備をゼロから開発し、生産効率を上げていった挑戦の裏には、物作りを追求する素材メーカーらしい地道な努力があった。
【関連記事】ユニクロのリサイクルダウン 東レが全自動設備を開発
ULDは、戦略的パートナーシップを結ぶ東レとユニクロにとって象徴的なアイテムの一つだ。軽くて暖かく、コンパクトにたたんで持ち運べる。本格的な防寒アウターとは違う羽織り感覚のダウンウェアは、インナーや部屋着など人びとのコーディネートを変えるほどのヒット商品となり、シリーズを継続している。
あきらめかけた案件
一方、ダウンは丈夫で繰り返し使える素材であるものの、世の中でリサイクルされている商品はごくわずか。原料調達の視点で見ても、供給量や価格が不安定だったり、動物愛護の流れで将来にわたってバージン原料が使えるのか不透明さも抱える。東レGO事業部の大川倫央GO事業第2室長は、ユニクロ出向中の14年にULDのリサイクルが出来ないか検討したことがあったが、効率良くダウンを取り出す手段がなく、コストも合わないことがわかって一度はあきらめた案件だった。
しかし年々、CSR(企業の社会的責任)やサステイナブル(持続可能な)の機運が高まるなか、「これを実現させるのは、メーカーとしての東レの役割」と改めて思いを深め、18年に再度チャレンジを始めた。頼ったのは社内で設備開発を担当するエンジニアリング開発センター(E開センター)、生産技術を担当する繊維加工技術部(加技部)だ。
一般的なダウンリサイクルの手法は、手作業で取り出すものがほとんど。ダウンがたっぷり詰まった羽毛布団やダウンアウターだと一度の作業で多くのダウン、フェザーが取り出せるが、1着200グラム強のULDから取り出せるダウンは50グラム程度。一着ずつ手作業したのではコストが合わず、機械化を実現しなければプロジェクトは前に進まなった。
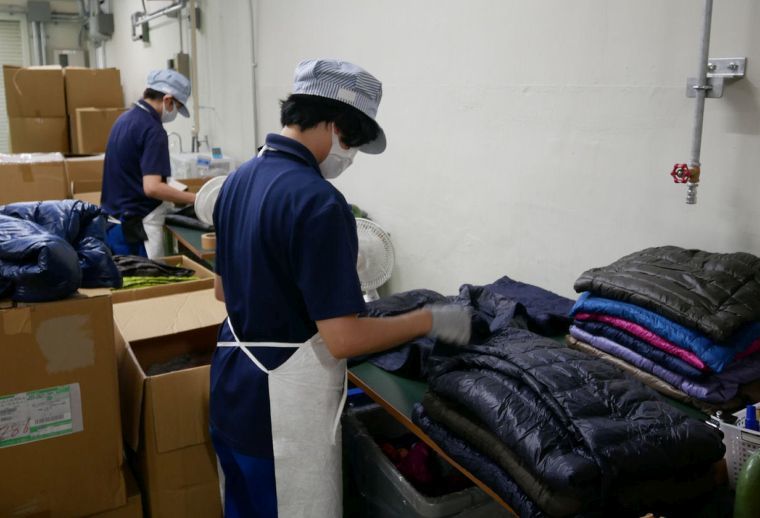
開発センターの知見
E開センターは、あらゆる事業に関わる生産設備を開発し、繊維では合繊紡糸、織物などの製造装置を扱う。繊維装置を担当する第1開発室の岡尚樹部員は機械化の依頼を受け、参考になるようなダウンリサイクル機械を世界中調べたが見当たらず、「一からどころか、ゼロからの開発だった」と振り返る。
そこでプロセスを検討し、機械を試作。①製品を切断②風で攪拌(かくはん)しながら軽いダウン、フェザーだけを分離③圧縮して詰める、という量産機のベースとなる三つの工程が固まり、カットなどのロスを除くとダウンの9割ほどをリサイクルに回せる仕組みが見えた。これを実現したのはE開センターの幅広い知見だ。ファスナーもろとも裁断する強力な刃は、炭素繊維複合材のノウハウ。風の流れは、ポリマーなど流体を分析するコンピューターシミュレーション技術が生きた。
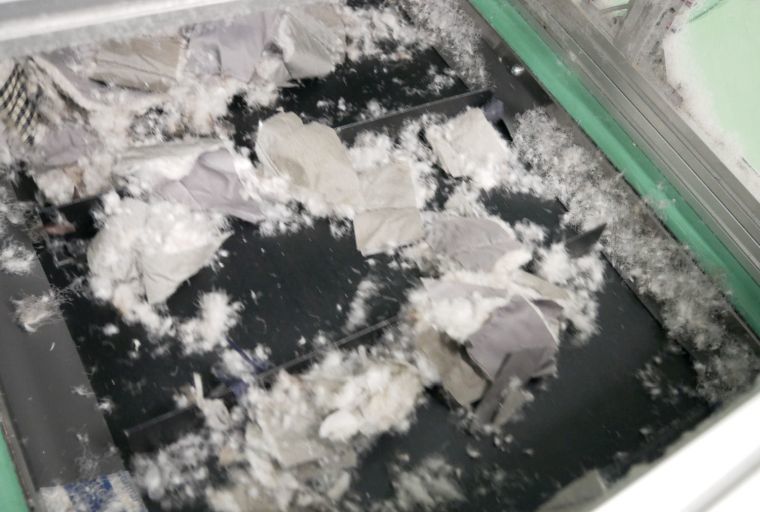
こうしておそらく世界初の装置が完成し、今年5月に稼働を始めた。しかし、これ以降も苦労の連続だった。まずは月3万着を目指して動き出したが、日に数十キロしか処理できず、5月は2万着にとどまった。1日に何度もメンテナンスで設備を止めなくてはならず、装置内で起こる裁断片の絡まりなどの原因を探った。
装置の立ち上げ以降を担当する加技部グローバルSCM技術室の藤田和哉担当課長は、「トラブルの原因をつきとめるため、5月ごろは機械の前にずっとはりついて動きを観察した」という。週1回、E開センターとのミーティングで原因究明と解決策について共有し、それをクリアして生産スピードを上げると、次のトラブルに直面する、を繰り返しながら6月は倍の4万着を達成、7月は2交代に増やして目標の6万を上回る8万着近くに伸ばした。
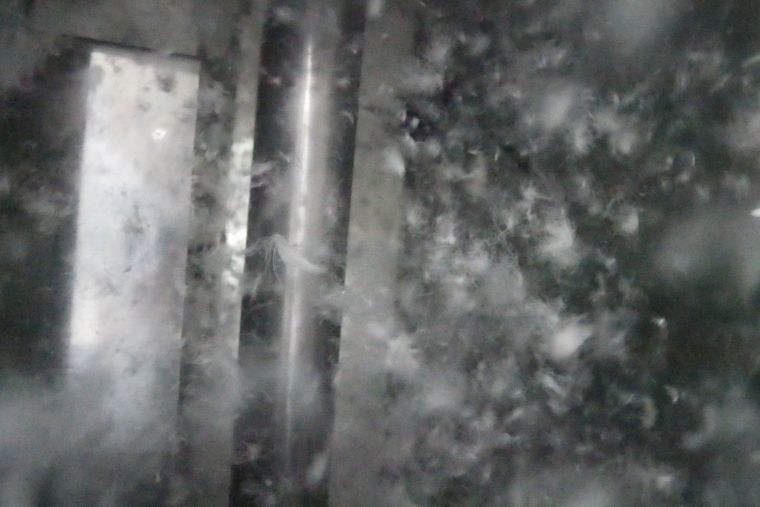
ナイロン再生も検討
現在の目標は、現状の2交代のまま月10万着に引き上げること。そうすればリサイクルでもコスト競争力が高まり、経済性とサステイナビリティーを両立した仕組みが可能になる。
また、現在は廃棄している裁断くずをリサイクル出来ないか追求していくのも、素材メーカーとしての役割だ。ダウンを取り除くと1着当たり150グラムほどのナイロン生地や、ファスナー片などが出る。ナイロンのリサイクルは東レが過去から知見を持っており、付属、縫い糸などとの分別方法を検討しながら、ナイロンの循環も視野に入れる。
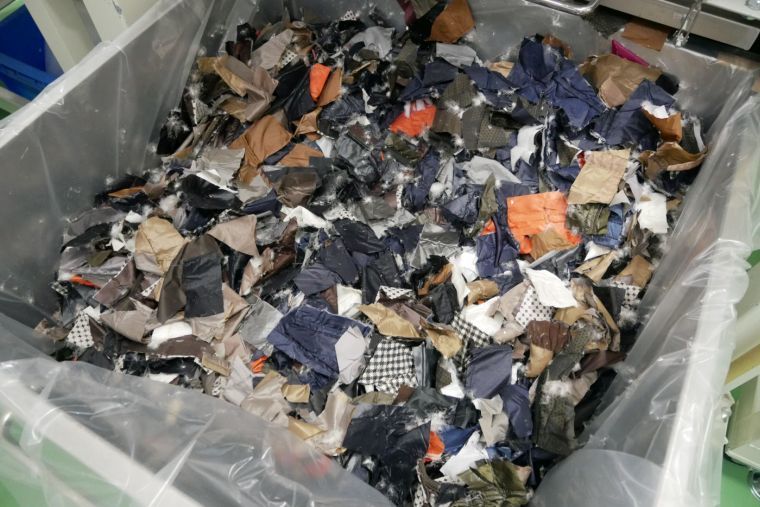
《チェックポイント》コストダウンを徹底的に追求
ダウンリサイクルを事業化するため、東レは徹底的にコストダウンを追求した。2交代でどこまで生産性を上げるかはもちろん、倉庫代や輸送コストまで考え抜かれている。
例えば10キロのダウンを梱包(こんぽう)する箱は、15箱で10トントラック1台に収まり、コンテナサイズでそのまま神戸から洗浄処理を行う台湾へ輸送される。
大川倫央GO事業第2室長が「ぜひ注目してほしい」と強調したのが、建屋だ。使われずに残っていた古いのこぎり屋根の工場跡を利用したもので、これもコストを追求した結果だ。
サステイナビリティー(持続可能性)の重要性が指摘されるが、慈善事業では企業の取り組みは続かない。真に持続可能なものにするには〝経済合理性〟という視点が欠かせないと改めて気づかされた。
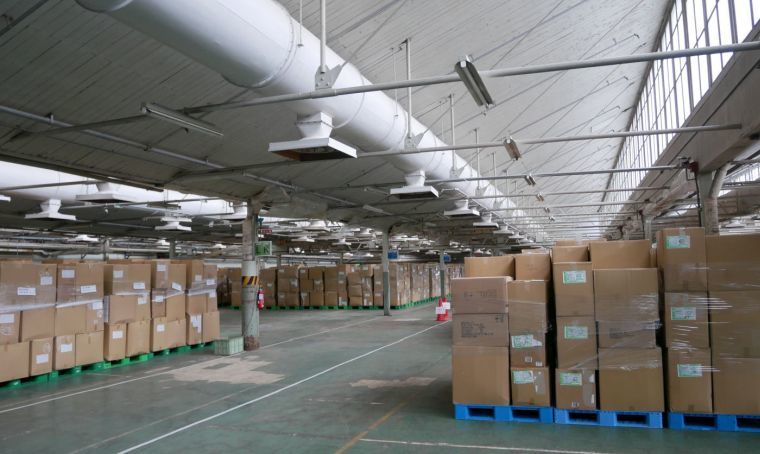
《記者メモ》素材メーカーの強さの源泉
世界有数のSPA(製造小売業)と日本を代表する合繊メーカーが組んだダウンリサイクルが本格始動し、今秋から商品化がスタートする。第1弾だけで62万着回収という量は、世界的にも注目される大規模なリサイクルプロジェクトだろう。ウルトラライトダウンという定番ヒットアイテムがあったからこそ成立したといえるが、仕組み作りの面では、素材メーカーとしての東レのDNAが大いに発揮されたプロジェクトだったと取材を通じて感じさせられた。設備がなければ自作し、壁につき当たれば粘り強く解決に挑む――そんな地道な姿勢からは素材メーカーとしての強さの源泉を垣間見た。
(中村恵生)
(繊研新聞本紙20年10月7日付)