日本有数のニット産地、山形。佐藤繊維はこの地で、牧羊と手編み用毛糸の手紡ぎから始まった。今では国内外の有力ブランドを顧客に持つ、日本最大のニットメーカーだ。紡績からニット生産、自社ブランドの製造・販売、セレクトショップやレストランの運営と業容を拡大してきたが、一貫して「世界にない」(佐藤正樹社長)を追求している。糸作りや編み立て、デザインの各段階で磨いてきた独自性を商品開発に生かし、次々に新たな販路を開いている。
トレンドを追わない
創業は1932年。当初は「目立つ特徴もなく、山形では100番目くらいの小さな工場」だったが、今ではグループ会社を含め、従業員数は400人を超える。
コンピューター横編機は70台を所有し、対応ゲージは3~16ゲージと幅広い。その背景に、今の佐藤繊維の原点が見えてくる。
30年前までは7ゲージ専門だったが、佐藤社長の入社を機に、先代の父が10ゲージの機械を7台購入した。ハイゲージの人気が高まりつつあったことを受けた投資だった。しかし、実際に市場で主流になったのは、さらに目が細かい12ゲージ。機械は返品できず、佐藤社長は「10ゲージの機械で注文をとるしかない」と決意、残った糸で変わった編地を作ることにした。
例えば、7ゲージの適正番手に近い太い糸を使い、限界まで度目を詰めたニット。素材や番手を変えて様々な編地を試作し、面白いものができると注文が入った。ニット事業は5年で黒字を達成。その後5ゲージ、12ゲージ、14ゲージ、3ゲージとバリエーションを増やしていくが、トレンドは追わず、あくまで開発で受注を獲得する方針を貫いた。「トレンド商品でシェアをとっても、それは誰かのビジネスでもうけているだけで、自社のビジネスにはならない」。洗えるエクストラファインメリノウールのハイゲージニットを例にそう話す。30年以上前に欧州で生まれ、日本にも人気が波及、一時は国内紡績、ニットメーカーも潤ったが、たちまち労働コストの安い中国に生産が移っていった。
紡績事業は、廃業した協力工場を相次ぎ引き取ったこともあり火の車だったが、20年末に愛知県一宮市のサンファインから大型トラック30台分もの紡績設備を買い取った。多様な機械がきれいな状態で残っており、10年後も紡績事業を続けるなら「今買うしかない」と踏み切った。
ミュール精紡や英式紡績、トライスピンなどを集約した本社工場は高付加価値品に特化、グループ会社の月山紡績は大量生産・低コストの工場として生産戦略を見直し、体制を整えた。転機はその矢先。中国のロックダウン(都市封鎖)、減産や在庫縮小を背景とした糸不足で、注文が殺到し、半年以上先まで予約で埋まった。
この流れを一過性の盛り上がりに終わらせず、さらに発展させるべく、増産と効率化へ歩みを進めている。
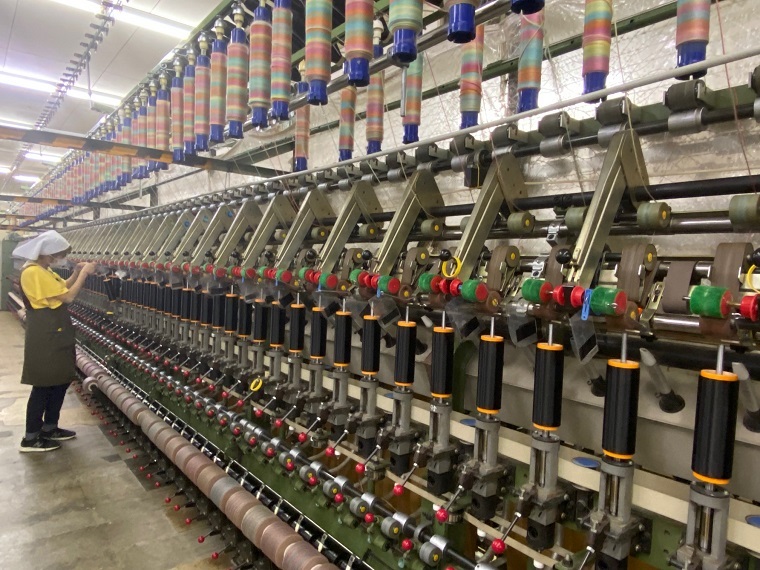
紡績からの開発力武器に
佐藤繊維の独自性は、糸からの製品提案に象徴される。蓄積された原料、紡績、ニット製造、パターンの知識とマーケティング機能を有する同社ならではであり、最近は機能合繊などと組み合わせた新たな糸で、海外の大手アウトドア・スポーツアパレルなどとの取り組みが増えている。
例えば、アウトドア向けのプルオーバー。米国では「世界で一番硬い」ことで知られる米国の高強力ポリエチレン繊維「スペクトラ」を芯に使い、ウールで巻いて風合いを柔らかくした。ウォッシャブルウールは、わた加工により、スケールを残したまま洗える機能を付与。防縮性を高めるために除去することが多いスケール(羊毛の表面を覆ううろこ状の構造)を残すことができるため、ウール本来の吸放湿性や撥水(はっすい)性を損なわない。さらに、再生ポリエステルと混紡した。
仮撚りポリエステルと和紙の特殊撚糸はさらりとしながら、和紙特有の硬さはなく、適度な膨らみがアウトドアメーカーのパーカなどで好評だ。
こういった特殊な糸を無縫製ニット「ホールガーメント」(WG)にして提案し、アウトドアやスポーツなどで採用が増えている。
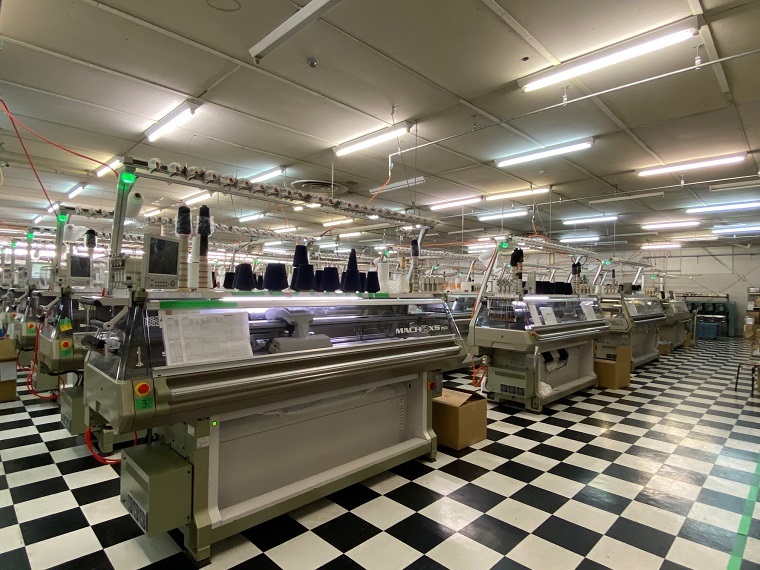
佐藤繊維は5年前に廃業した紡績工場を改装し、WG専用工場を新設した。当初52台だったWG機は、現在70台まで増設。紡績からの開発力を武器に、ローゲージからハイゲージまで揃える。WGの工場としては後発ながら、自社のトップパタンナーによる高度なプログラム開発で、複雑なシルエットも可能にした。WGは全自動のため、効率を追い求めて決まった糸を用いる工場が多いのに対し、佐藤繊維は特殊な糸を使うことで差別化する。この秋のミドラーに採用されたウールフリースは、ウールのループヤーンを使ってフリースの柔らかさを表現しつつ、インナーにも向く薄さにした。本来は機械に通らない糸で、糸から改良を重ねたという。
編みにくい糸のため、工場の環境も徹底的に管理する。湿度をコントロールする機械は、半導体部品の製造工場にも使われる上位機種を設置した。
足元ではインナーブランドとのプロジェクトが進行しており、今後インナーに向く機種10台を追加する予定だ。
《チェックポイント》高品質は従業員の意識から
高い品質を作り続けるために必要な要素は様々あるが、作業環境は最も大事な一つだろう。いくつか産地の工場を訪れたことがあるが、佐藤繊維の工場は圧倒的にきれいに見えた。取引先などからも、よく驚かれるそうだ。
例えば、繊維くずがたまりがちな編機の裏側も、クリーンに保たれている。ホールガーメントに編み終えた製品が何枚もとどまっているということもない。
佐藤繊維の工場にある機械は、廃業した工場から譲り受けたものも多い。運び出しや組み立てといった作業は、主に従業員が行う。ある紡績工場を引き継いだ時は、買収の手続きに時間がかかり、工場に入れたのは倒産から1年が過ぎたころ。浸水で床が上がり、機械はさびついて8割は動かなかったそうだ。それを従業員が直し、ぴかぴかに磨き上げ、10カ月後に復旧させた。自らが手をかけた機械は、清潔を維持したい気持ちも強まる。従業員一人ひとりの意識が作業環境の改善につながっている。
《記者メモ》後継者の存在
「機械が壊れたら、紡績事業をやめよう」。最近までそう考えていたそうだ。糸からの提案の核となる事業だが、単体では赤字続き。コロナ禍にになってからは雇用調整助成金を受給し、工場は週2回しか稼働していなかった。
サンファインウールから機械を買うことを決めたのは、それから間もなくのこと。きっかけは、長男が家業を継ぐために戻ってくるという知らせだった。「今買わなければ、10年後には紡績ができなくなる」との思いに駆られたという。苦悩や葛藤もあったはずだが、「息子に継ぐとなったら何歳になっても頑張れる」と明るく笑った。
後継者は単に経営権を引き継ぐ存在ではない。現経営者が目の前の苦難を乗り越え、再興を目指す原動力になる。そして、佐藤社長の入社時のエピソードのように、成長の源泉も生むのだと実感した。
(橋口侑佳)
(繊研新聞本紙22年9月7日付)