東レの「ナノデザイン」は、同社が開発した合成繊維の新しい製造方法。この技術を使うと、これまでできなかった極細の糸や、変わった断面形状、異なる原料を組み合わせた糸などが作れ、新しい機能や風合いが生み出せる。実際にナノデザインを使ったテキスタイルが16年以降に発表され、撥水(はっすい)性能を高めた繊維や、本物の絹のような合繊が販売されている。
【関連記事】【この技術がすごい④】インクジェットプリント
◇複合技術から飛躍
通常、ポリエステルやナイロンは溶融紡糸で作られる。温度を上げると溶け、冷やすと固まる性質(熱可塑(かそ)性)を持つため、熱で溶かしたどろどろの原料を細い穴から押し出し、高速で引っ張って細く強くしながら、冷やして繊維にする。ナノデザインも溶融紡糸には変わりないが、独自開発した紡糸プロセスがポイントになっている。
合繊を紡糸する際、原料を押し出す穴の部分を口金といい、口金の形を変えることで繊維の断面形状も変化させられる。丸い穴からは丸断面、三角形の穴からは三角断面という具合だ。また、穴の大小を変えることで、糸の太さもコントロールできる。これは、ところてん突きをイメージするとわかりやすいかもしれない。
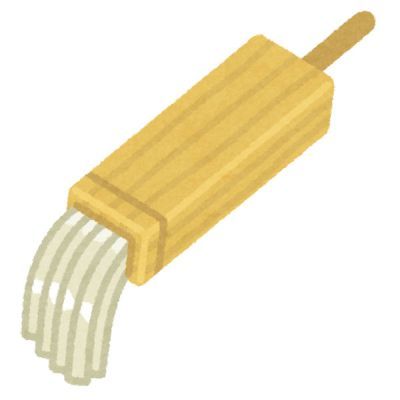
ただし口金から出た時の原料は液状なので、正三角形の穴から押し出されても徐々に固まっていくため、角がとがったきれいな三角にはならないし、作れる糸のバリエーションも限界がある。
そこで高機能・高付加価値の合繊作りのために発展したのが、2種類の原料を組み合わせた複合繊維だ。例えば、1本の丸断面の繊維を放射状に分割することで角をくっきりとがらせた三角状断面を作り出したり、海島紡糸(海にいくつも島が浮かんだような断面構造。海成分にアルカリで溶解しやすい原料、島に通常の原料を配置し、紡糸後に海成分を除去すると島の極細繊維が取り出せる)によって作られたマイクロファイバー、半月状の2種類の成分が貼り合わさったサイド・バイ・サイド糸、芯と外側が異なる成分で出来た芯鞘(さや)複合糸、真ん中が空洞の中空糸など、日本の合繊メーカー各社の開発努力によって多くの糸が作られるようになった。
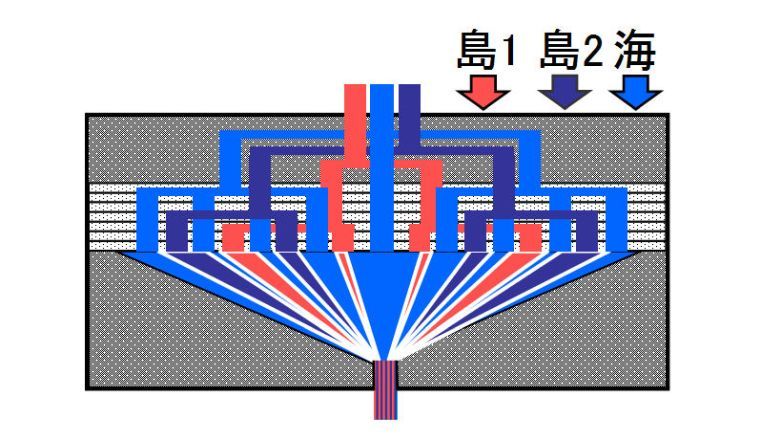
複合繊維は、異形断面だとワイピングクロスに使用したときのふき取り性能が丸断面と比べてアップしたり、W字断面で毛細管現象によって汗や水を素早く吸って拡散させたり、中空糸は軽量性や保温性に優れるなど機能や風合いが向上する。サイド・バイ・サイドは熱で縮む性質(縮率)が異なる2種類の成分を貼り合わせているため、加熱によって糸がスプリングのような形状になり、伸縮性が生まれる。
◇極限までポリマー分割
これらに対しナノデザインは、発想の転換と精密技術の導入で合繊製造技術を飛躍させた。ナノデザインでは口金から吐出する前の段階で、液状の原料の流れをいくつにも分割し、口金の好きな場所から狙った成分を吐出することができる。原料を分割する役割を果たすのが分配板で、従来にはなかった手法だ。
原料ポリマーを極限まで分割する分配板の働きによって、断面形状をナノサイズでコントロールでき、例えば直径150ナノメートルのナノファイバーや、三角やY字、六角形の均一なナノファイバーが作れるなど、あらゆる断面や太さの糸が作り出せる。
また、これまでできなかった異なる三つのポリマーを複合することも可能になった。ところてんの例えで言うと、切り口の断面がずっと細かくなり、しかも3種類の味がランダムな穴から出せるようなものだ。これによって、例えばアルカリに溶けやすい海成分と、ポリエステル、ナイロンという異なる種類の島成分で構成する糸や、島成分がバイメタル(性質の異なる2種類の繊維を貼り合わせた)構造のナノファイバーなども可能となり、原糸設計の自由度が高まった。
東レは16年に発表したファッション用素材「uts‐FIT」(ユーティーエス・フィット)で初めてナノデザインを市販品に採用し、その後もバリエーションを広げている。ユーティーエス・フィットは、56デシテックス・300フィラメント(1束300本の繊維で構成される56デシテックスの糸。1本の繊維=単糸は0.19デシテックス)の糸を使い、バイメタル構造の単糸によって捲縮(けんしゅく)が生まれ、光沢を抑えた見た目と、かさ高性や伸縮性を持つ。
このほか、繊維側面に深い溝を持ち、溝の空気によって撥水性能を高めた「ナノスリットナイロン」、絹のような上品な光沢や絹鳴りを再現し、合繊ならではの取り扱いやすさや機能性を持たせたシルキー素材「Kinari」(キナリ)などこれまでの常識を超えた繊維が次々と生まれている。
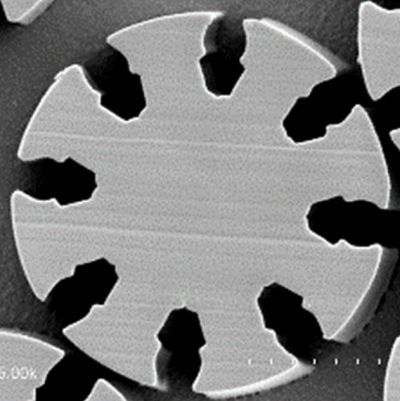
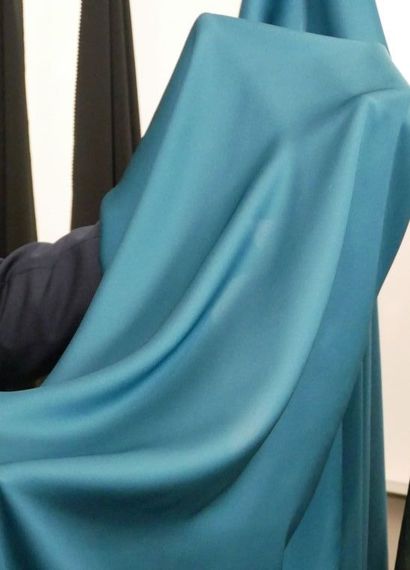
(繊研新聞本紙20年3月25日付)